Selecting breathing protection
When all other measures have been taken to reduce dangerous levels of exposure, respiratory protection is the last but important step to prevent harmful air contaminants from entering the body through the airways.
The employer is responsible for the selection, maintenance and provision of breathing protection equipment and its use in the workplace. The user is in his turn responsible for using it according to the employer’s routines. A programme designed to protect employees from exposure to air contaminants is described in the EN 529 guidelines: recommendations for the selection, use, care and maintenance of respiratory protection equipment.
Face fit testing
To maximise on the correct protection from respiratory equipment, it is crucial to ensure that it fits the user to an optimum level. Air will always take the path of least resistance, so any small gaps between the face and the respirator will result in reduced protection for the wearer. It is crucial to their safety that the user has a suitably sized and positioned respirator, which they know how to correctly fit.
Why undertake a Face Fit Test (FFT)?
Sundstrom recommends that any half or full-face mask user undergoes a Face Fit Test. Such a test ensures the correct comfort, fit and protection obtained whilst the user is wearing a face mask. One size does not fit all, and the mask must have a suitable and effective fit for you! Facial hair and jewellery, scars or outstanding facial features can all significantly detract from the performance of a respirator. In order to ensure that there is not leakage between the face and the respirator, leading to potential health issues, the face fit test is used to ensure an adequate seal has been achieved.
Exposure to even low levels of particles, gases and vapours can cause permanent and irreversible damage to the lungs and other vital organs. The importance of correctly protecting against these contaminants over an entire working career has become more apparent. A face fit test ensures that the RPE is both fit for purpose and acceptable to the wearer. In some markets it is a legal requirement, whilst in others it is only a guidance.
Carefully check the regulation that applies to you!
4 Things to Consider
1. Identification
Which hazardous gases, vapours, dust, smoke or aerosols do we need to protect ourselves from? Make workplace measurements and monitor the concentrations of the hazardous substances.
2. Risk assessment
Is sufficient oxygen level present during the entire period of exposure? What are the effects on health of the substances present? Are there any occupational exposure limits for these substances? Are there any other risks, such as splashing, sparks or explosive mixtures?
3. Selection of breathing protection
Half mask, full-face mask, powered or air-fed respirators.
4. Training
Fitting, function checks, donning, storage and maintenance. Routines for cleaning and replacing filters and wearing parts.
Good to know before you make your choice
There are many factors that need to be taken into account when choosing the right protection. Below we cover important information that may influence you in your choice of the right protective products.
Two types of breathing protection
1. Filter protection
Where the surrounding air passes through filters that remove contaminants. This type is used where sufficient oxygen level is present and known contaminants can be captured in the filter. The contaminants must have clear warning properties in the form of odours or taste in concentrations below the occupational exposure limits. Filters must not be used where the contaminant concentrations are Immediately Dangerous to Life and Health.
Examples of filter protection are half and full face masks with replaceable filters as well as powered-assisted filter protection for half and full masks or hoods, visors and helmets. For contaminants in gas form, appropriate gas filters are used with active carbon that absorbs the gas. As the filter becomes saturated the gradual breakthrough starts, therefore it is important to set up a filter replacement policy.
Particles such as dust, smoke and mist are captured in particle filters. As the degree of clogging rises, breathing resistance increases and the filter must be replaced if it is damaged or breathing becomes difficult. Combination filters are used in the presence of both particles and gas.
2. Breathing apparatus
Supplies the user with air from an independent source, via cylinders with compressed air or breathable air from a compressor. Continuous flow air line equipment with hoses is used in half and full face masks, hoods, helmets and visors.
Compressed air-fed breathing protection may be used in all environments suitable for filters and in which a higher level of protection is required. Some substances can not be adsorbed in filters, and in such cases compressed air-fed breathing protection is the only alternative.
The inhaled air must conform to EN 12021 and as an example not exceed the odour threshold for oil (0.5 mg/m³).
Work duration and workload
For short term jobs with low workload, a negative pressure mask can be used, i.e. half and full face masks with replaceable filters. To avoid harmful leakage into the mask, the fit to the face is important, as inhaling produces a negative pressure in the mask. High inhalation resistance due to large filter combinations contributes to further negative pressure as well as an increased breathing effort.
Long term work with high workloads often requires powered-assisted filter protection. A battery driven fan sucks the air through the filter and blows it into the face piece, which may be a loose-fitting visor, helmet or hood, or a tight fitting half or full face mask. The air flow of the equipment is important to maintain a positive pressure in the face piece, even during deep inhalation, especially with the use of loose fitting visors, helmets or hoods.
High workloads and contaminants with poor warning properties are examples of situations in which compressed air line equipment is appropiate. The compressed air is supplied from a compressor via an air line filter unit and hose to a belt-mounted regulating valve, to the half or full face mask or helmet, visor or hood.
Protection factor
All types of breathing protection have a specific protection factor that describes how efficiently they reduce the level of the contaminant in the air, i.e. inside the face piece.
The Assigned Protection Factor (APF)
is based on measurements inside and outside the protective device, conducted on workers in real work environments.
The Nominal Protection factor (NPF)
is based on laboratory measurements in conjunction with approval of the protection equipment to the EN standard.
Calculation of the protection needed at the workplace should be based on the Assigned Protection Factor (APF). Check national requirements for assigned protection factors EN 529.
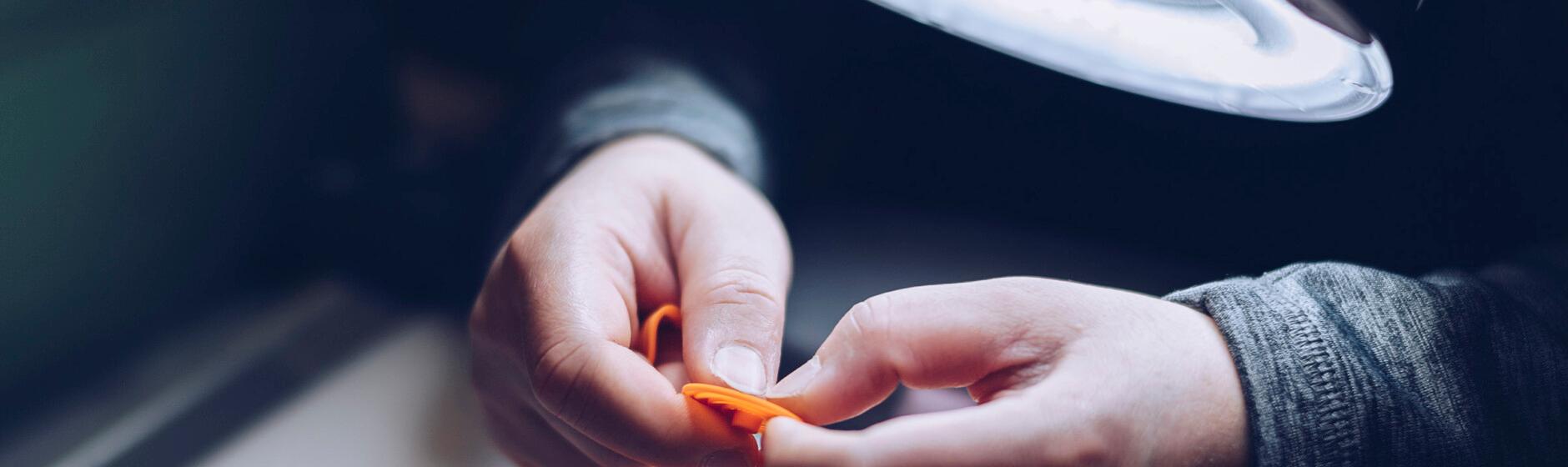
Two methods of fit test
There are two types of tests to verify the fit of a half mask.
Qualitative fit test
As the name suggest this type of Face Fit Test is objective. It involves placing a bag over the head of the wearer whilst wearing the respirator. A substance with a strong smell or taste (normally either Bittrex, giving a bitter taste, Saccharin, giving a sweet taste or banana oil with a strong banana smell) is added into the bag. If the wearer cannot smell or taste any of the additives, they are seen to have an adequate seal. This methodology can be compromised if the wearer has an impaired sense of smell or taste, a cold, or other sensory issue. It is also only suitable for use with half masks!
Quantitative fit test
This is a much more accurate and sensitive test giving a definitive number of particles inside the mask whilst undertaking several exercises. It also measures the particle count outside the mask and calculates a specified ratio between the two.
By comparing both figures you can obtain the measurable level of protection given by the mask. There are a number of ways of performing the quantitative test but all show a more tangible and effective conclusion, offering greater confidence in use.
This type of test can be used on both half masks and full-face masks.

Choose a suitable filter
Sundström Safety have a range of gas filters, particle filter and combined filter.
Choose a suitable filter for your work and environment. The gas filter can easily be combined with a particle filter
Particle Filters
For half and full face masks are divided into three classes depending on how effectively they can separate dust, mist and aerosols. Colour code – white.
A highly efficient filter such as the SR 510 P3 R offers protection against all types of particles such as dust, fume, fog, spray, asbestos even bacteria, viruses and radioactive dust.
A higher class also covers the lower ones, i.e. P3 covers both P1 and P2. The filters are replaced when the particle filter leads to increased breathing resistance. Particle filters offer protection only against particles.
Protection Classes with Respect to Efficiency (EN143) |
(NaCl and paraffin oil) |
---|---|
P1 R/NR solid and wet particles | 80 % |
P2 R/NR solid and wet particles | 94 % |
P3 R/NR solid and wet particles | 99,95 % |
”R” after the class means that the particle filter can be reused. ”NR” after the class means that the particle filter must not be used for more than one shift.
Gas Filter
For half and full masks are divided into three classes on the basis of their capacity and test concentration.
Filter Class (EN 14387) |
Tested in Concentrations |
---|---|
1 | 0,1 percent by volume = 1000 ppm |
2 | 0,5 percent by volume = 5000 ppm |
3 | 1,0 percent by volume = 10000 ppm |
ppm=parts per milion
Filter Type | Protects Against | Color Code |
---|---|---|
A | A Organic gases/vapours with a boiling point above 65ºC, e.g. solvent naphtha, toluene, styrene and xylene | ![]() |
B | Inorganic gases/vapours such as chlorine, hydrogen cyanide and hydrogen sulphide | ![]() |
E | Acidic gases/vapours such as sulphur dioxide and formic acid | ![]() |
K | Ammonia and certain amines | ![]() |
AX | Organic gases and vapours with a boiling point below 65ºC, such as acetone, methanol and dichloromethane | ![]() |
HG-P3 | Mercury | ![]() |
Gas filters afford protection only against gases.
Combination Filters
Combination filters are used when gases/vapours occur simultaneously with particles, e.g. in high-pressure cleaning, spray painting, heating substances or gas condensation. Select an appropriate gas filter and combine it with a particle filter by simply pressing them together or use filters with a fixed gas and particle filter in one.